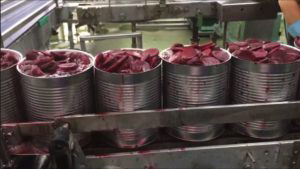
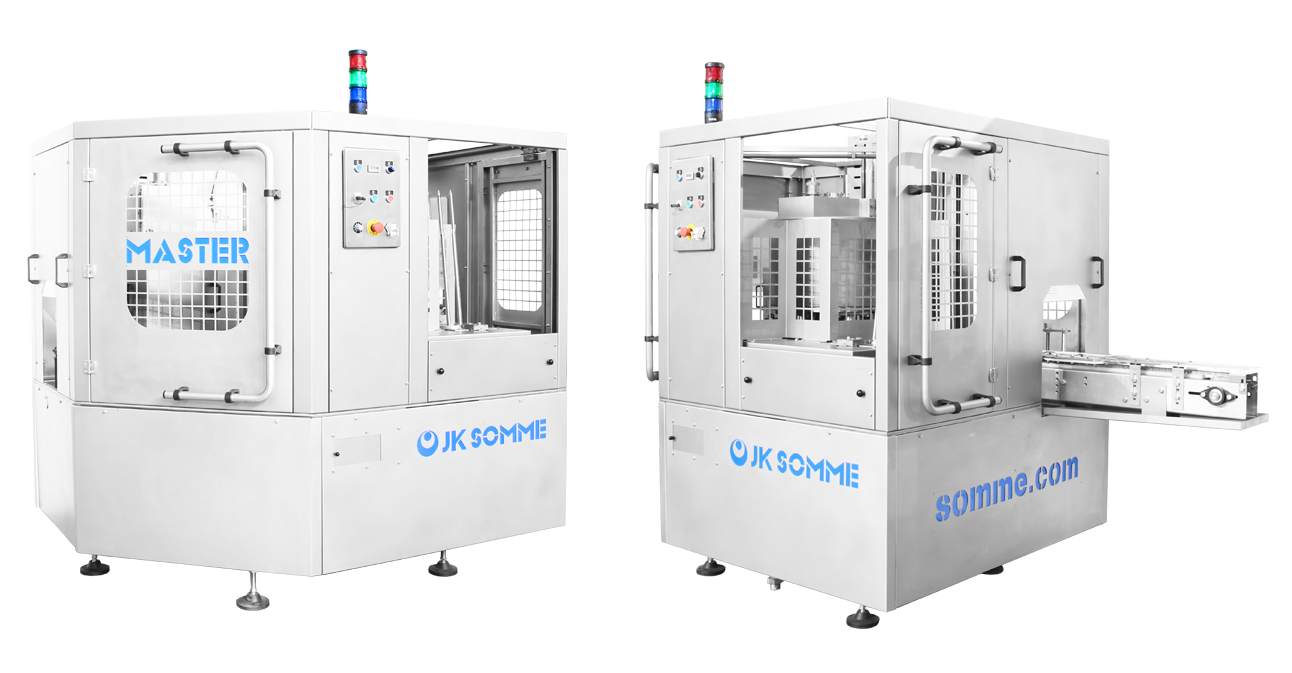
SUPERIOR PERFORMANCE
Fastest single head seamer on the market
cans/min
cans in an 8hrs shift
cans in a month
cans in a year
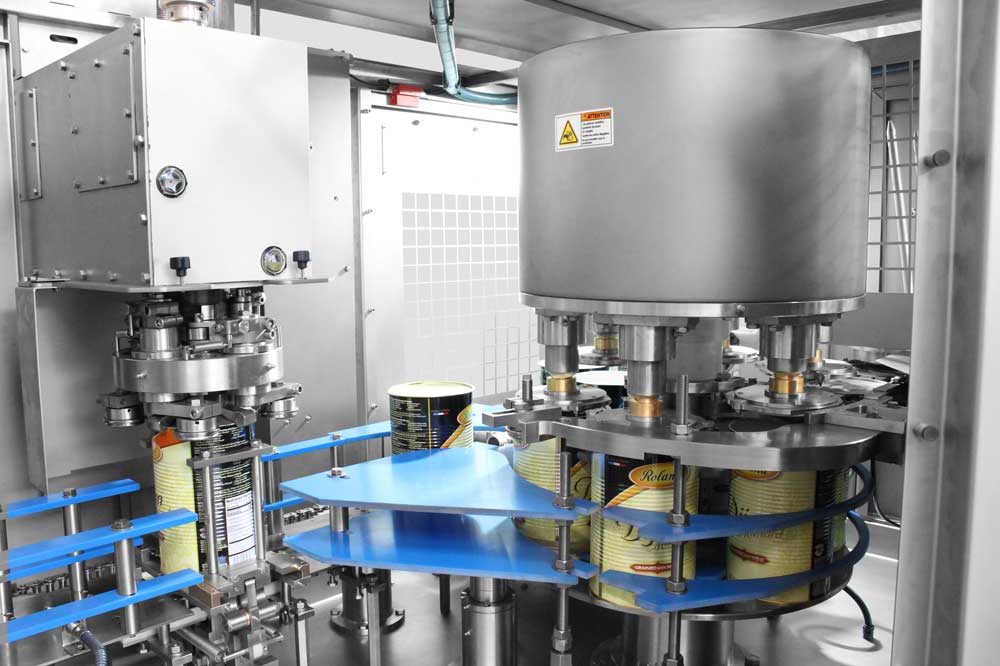
ROTARY CLINCHER FOR OVERFILLED CANS
It acts as a can topper, pressing down and fitting any protruding product back into the can. It acts also as a guillotine, cutting off sardine tails, octopus tentacles or pieces of meat that hang over the edges of the cans.
-
The clincher separates and feeds each lid accurately onto each can body. With 6 stations, process is continuous, slow & precise.
-
Pushes and fits overfilled product into the can.
-
After that displaces the excess of oil, brine or sauce from each can before seaming.
-
Clinches and holds every lid onto its can body at two opposite points.
Safest and most effective rotary clincher on the market when canning complicated products such as beetroots, carrots, sauerkraut, cucumbers, olives, whole peppers, confit de canard, octopus, corned beef, etc.
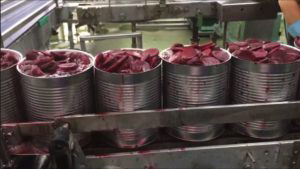
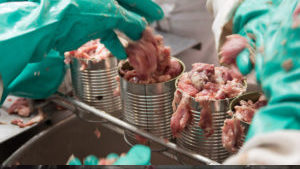
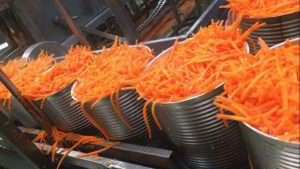
SPECIFICATIONS
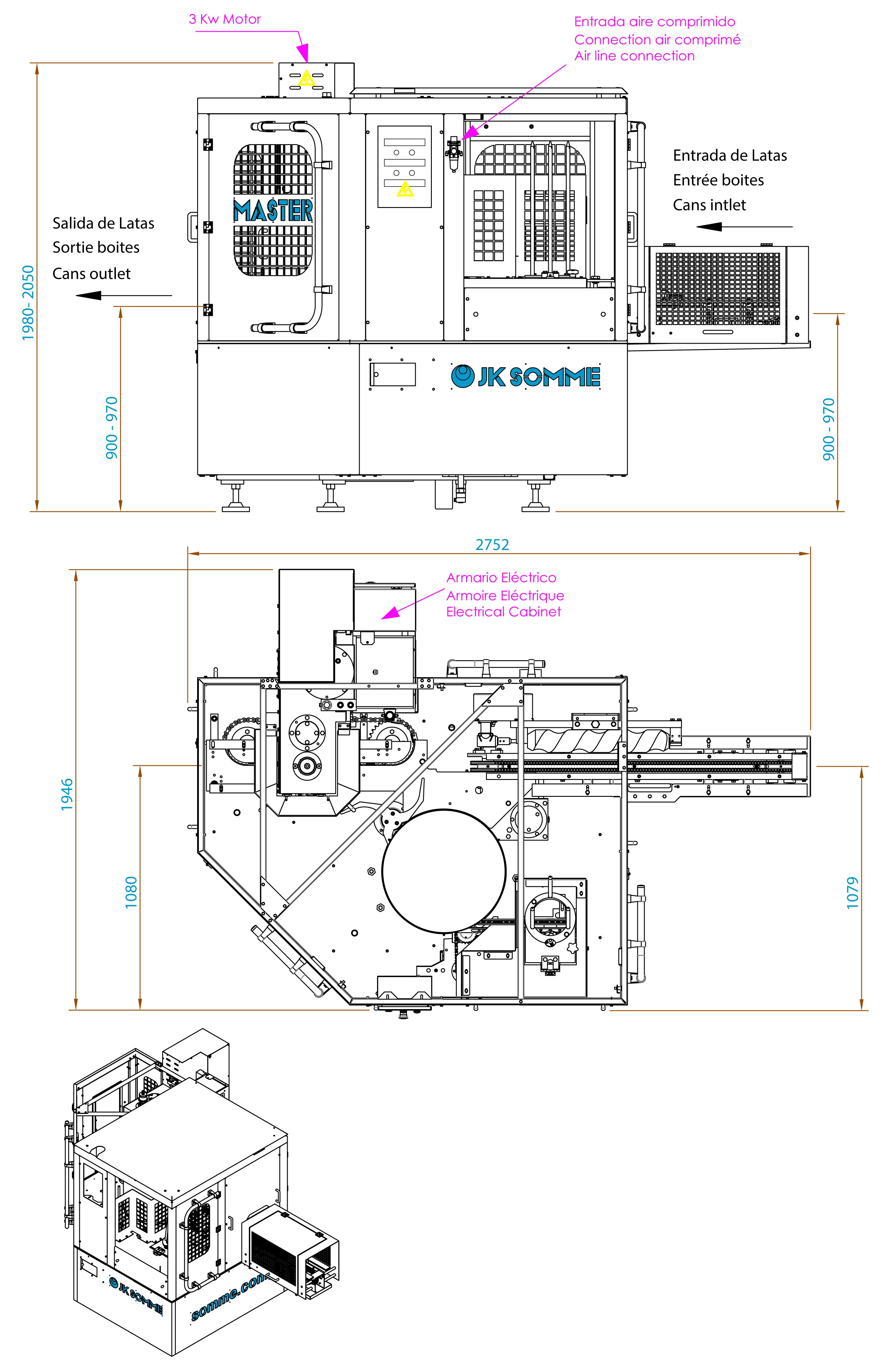
ACCEPTED CAN SIZES
-
Max. Diameter: 165 mm
-
Height Range: 15 – 275mm
KEY FEATURES
-
Rated speed: Up to 90 cans/minute
-
Seaming heads: Single
-
Can seaming op.: Still standing (cans don’t rotate)
-
Second operation off-seam setting: Yes
-
Main drive gear box: Oil bath
-
Lubrication: Grease
-
Easy maintenance & greasing: Yes
-
Can infeed & outlet: Straight line
-
Can entrance to machine: By timing screw
-
Clincher: 6 stations rotary clincher with vertical motion
-
Cover separator: Single knife
-
Mechanical protection against overloads: Yes
-
No can/No cover feed: Yes
-
Parts made stainless to optimize hygienic design: 80%
-
Safety enclosure: Stainless steel with door interlocks following CE safety regulations
-
Internal lighting of the complete working area: By LED lights
-
Stainless steel spillage collecting tray covering machine frame: Yes
-
Quick cleaning & water drainage: Yes
-
Electronic variable speed motor drive: Yes
-
PLC: Yes
-
Kit of recommended spare parts: Yes
-
Tool kit and instruction manual: Yes
PRACTICAL FEATURES
-
Estimated tooling changeover: 5 hours
-
Can height changeover: 10 minutes
-
Can pitch: 210 mm
DIMENSIONS & CONSUMPTIONS
-
Overall dimensions (LxWxH): 2.751 x 1.948 x 2.036 mm
-
Can feeding conveyor height: 912 – 992 mm
-
Net weight: 2.550 Kg
-
Motor: 4 Hp
-
Compressed air: 40 L/H 6 Kg/cm3
OPTIONAL FEATURES
-
Can making version: Yes
-
Filler connecting parts: Yes
-
Touch screen control panel: Yes
-
Mechanical cover marker for a max of 2 rows x 7 marks: Yes
-
Extended lid chute with vibrator: Yes